Understanding In-Mold Decorations: Strategies, Patterns, and Ideal Practices for Optimal Outcomes
In the world of production, the art of in-mold decors stands as a critical facet of product layout and manufacturing. As industries continually look for cutting-edge means to improve aesthetic appeal and capability, grasping the complexities of in-mold decorations has actually emerged as a crucial skill set. From selecting the best materials to including advanced layout patterns, the trip in the direction of achieving optimum results in this domain name is complex. By delving right into the methods, patterns, and ideal techniques that underpin successful in-mold decoration processes, services can open a world of possibilities that not just boost the visual allure of their products but additionally streamline manufacturing effectiveness and reinforce customer interaction.
Material Choice
Material option is an essential aspect of grasping in-mold decors, as it directly impacts the quality and toughness of the final item. When selecting materials for in-mold decorations, it is necessary to consider factors such as compatibility with the molding process, the preferred visual outcome, and the ecological conditions the item will deal with. Thermoplastic products like polypropylene, abdominal, and polycarbonate are typically utilized for in-mold decorations because of their versatility and capacity to accomplish complex layouts. These products provide excellent moldability, enabling producers to develop complicated forms and patterns with accuracy.
Moreover, the chosen material needs to have great adhesion residential or commercial properties to ensure that the design sticks securely to the substratum during the molding process. Adhesion between the product and the decoration is vital for avoiding delamination and making certain long-lasting visual appeal. In addition, products with high warm resistance are chosen for in-mold designs, especially for items that will certainly be revealed to elevated temperatures during their lifecycle. By thoroughly selecting the ideal material for in-mold designs, makers can improve the total top quality and durability of their products, fulfilling the expectations of both end-users and customers.
Design Development
A crucial consider advancing the area of in-mold decorations is the constant expedition and implementation of layout advancement techniques. Layout innovation plays a critical function in enhancing the aesthetic allure, capability, and total top quality of items manufactured utilizing in-mold design processes. By including cutting-edge design aspects, manufacturers can differentiate their items in the market, draw in customers, and stay ahead of rivals.
Among the essential elements of style technology in in-mold decors is the integration of elaborate patterns, structures, and graphics that were formerly testing to attain with standard design methods. Advanced modern technologies such as 3D printing and digital layout devices make it possible for designers to produce facility and in-depth layouts that can be seamlessly transferred onto shaped components. Additionally, making use of vivid shades, metallic coatings, and unique results like gloss or matte textures can further boost the aesthetic allure of in-mold decorated products.
Furthermore, layout technology prolongs beyond aesthetics to incorporate useful enhancements such as ergonomic forms, incorporated functions, and customizable elements that accommodate specific individual needs. By welcoming layout technology, manufacturers can open brand-new possibilities for product, personalization, and imagination differentiation in the affordable landscape of in-mold decors.
Production Efficiency
Reliable production procedures are important for equating the cutting-edge layouts established in the area of in-mold designs into high-grade completed items that meet market demands and consumer expectations. In the world of in-mold designs, manufacturing performance encompasses various vital elements that contribute to the general success of the production process. One important element is the optimization of mold design and tooling to make certain smooth and accurate decoration transfer onto the final item. By fine-tuning mold and mildew configurations and buying high-quality tooling materials, makers can improve performance and consistency in production.
Automation not only speeds up the production process but additionally improves precision and repeatability, leading to a more consistent and high-quality end product. Generally, an alternative method to manufacturing effectiveness is vital in making the most of the capacity of in-mold decoration methods and accomplishing optimal outcomes in the competitive market landscape.
Quality Assurance Actions
What are the essential strategies for ensuring strict top quality control actions in the realm of in-mold designs? Quality control measures are extremely important in in-mold decoration procedures to ensure the manufacturing of perfect and top notch finished products. One critical method is the implementation of rigorous evaluation procedures at every stage of the manufacturing procedure. This includes performing extensive aesthetic inspections, dimensional checks, and color uniformity analyses to determine any type of defects or incongruities beforehand.
Making use of sophisticated technologies such as automatic evaluation systems can also enhance the quality control procedure by supplying dependable and exact information for analysis. this contact form These systems can spot flaws that may be missed out on by manual inspections, consequently boosting general product quality and uniformity.
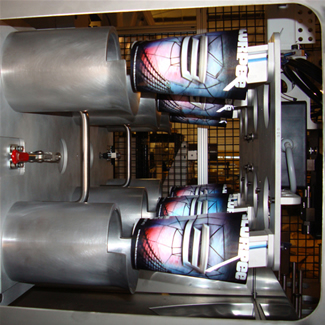
Normal training and growth programs for employees associated with the in-mold decor procedure can additionally add to keeping top notch requirements. By educating staff on ideal methods, quality expectations, and the importance of interest to detail, companies can cultivate a society of high quality consciousness throughout the company.
Customer Appeal
To enhance the marketability of in-mold design products, catering and recognizing to customer preferences play a vital role in identifying their appeal and success. Consumer allure in in-mold designs is influenced by numerous factors, consisting of layout looks, color selections, longevity, and total performance. Customers are progressively seeking individualized and special products that reflect their uniqueness and design. Supplying modification alternatives such as personalized layouts, shade variants, and textural elements can considerably boost the charm of in-mold design items.
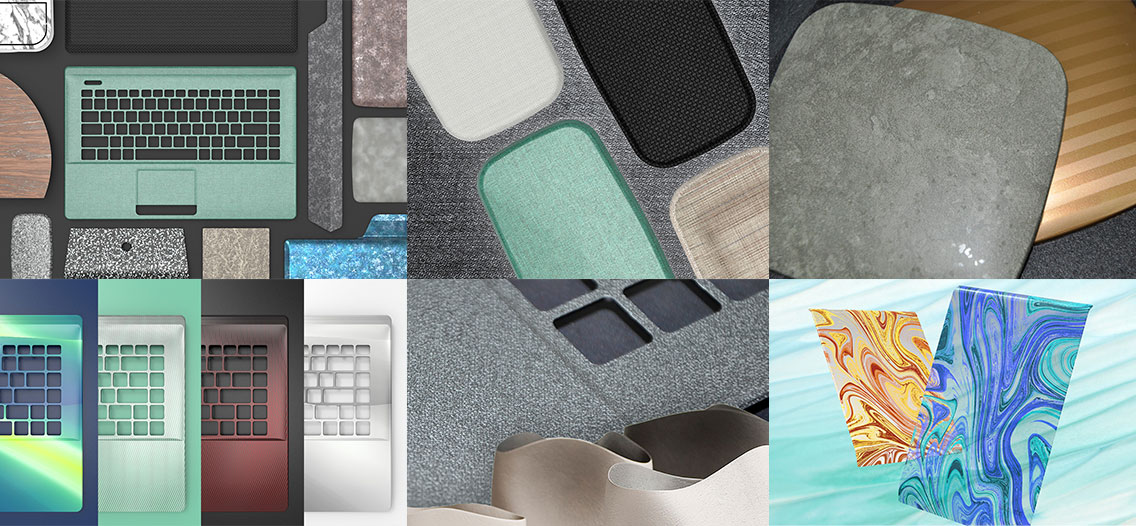
Final Thought
In-mold designs offer a efficient and functional way to enhance product appearances. Understanding in-mold decors needs an alternative approach that considers all elements of the manufacturing process to make certain success.
In the realm of important source production, the art of in-mold designs stands as an essential aspect of product style and production. Style advancement plays a vital role in boosting the aesthetic charm, performance, and general top quality of items manufactured utilizing in-mold design procedures.One of the key elements of style advancement in in-mold decors is the assimilation of detailed patterns, structures, and graphics that were formerly challenging to attain with typical design approaches.Effective manufacturing processes are necessary for translating the ingenious styles established in the area of in-mold decors right into high-quality completed products that satisfy market demands and consumer assumptions. Supplying personalization alternatives such as individualized styles, shade variants, and textural elements can considerably boost the charm of in-mold decoration items.
Comments on “In-Mold Decorations: Changing Production Specifications”